Understanding Heavy Equipment Costing for Transportation Services
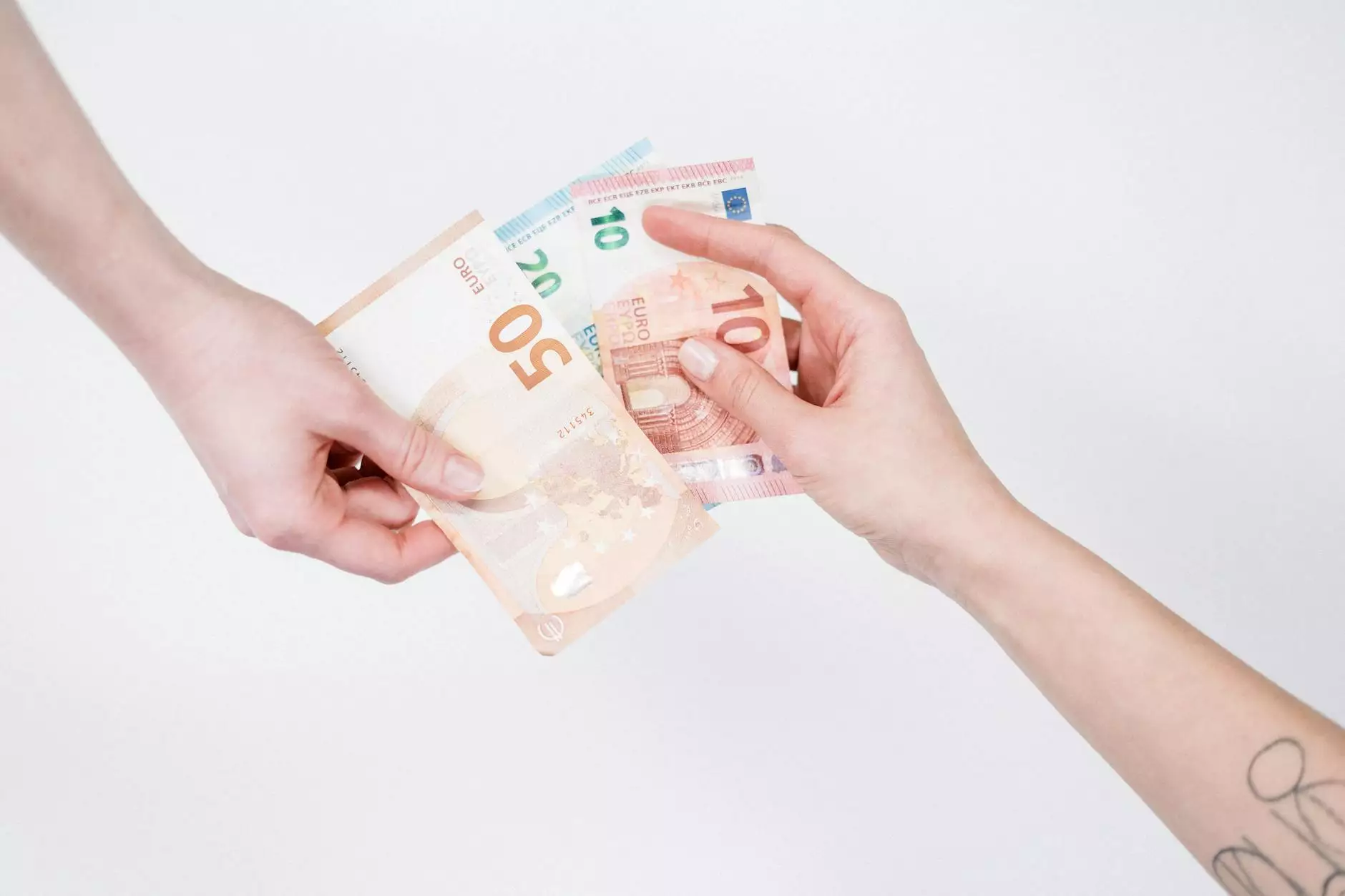
In the world of transportation services, particularly in sectors involving heavy equipment, understanding the financial implications is crucial. Heavy equipment costing is not merely about the purchase price; it encompasses a range of financial considerations that can significantly impact the overall profitability of a business. This article aims to provide a comprehensive overview of heavy equipment costing, specifically tailored for businesses involved in transportation, town car services, and vehicle shipping, like those at elevationtransportservices.com.
What is Heavy Equipment Costing?
Heavy equipment costing refers to the total financial expenditure associated with acquiring, operating, maintaining, and eventually disposing of heavy machinery. This includes not just the purchase price but also financing costs, operational expenses, insurance, and maintenance costs. Understanding these elements is critical for businesses to effectively budget and forecast their financial health.
Key Components of Heavy Equipment Costing
To accurately assess the costs associated with heavy equipment, it's essential to break down the various components:
- Purchase Price: The initial cost of acquiring heavy equipment.
- Financing Options: Loans, leases, or outright purchases influence long-term costs.
- Operational Costs: Fuel, labor, maintenance, and other ongoing expenses.
- Insurance: Protecting your investment against damages and liabilities.
- Depreciation: The loss of value over time, affecting the overall assets of a company.
- Disposal Costs: Costs incurred when selling or scrapping equipment.
The Importance of Accurate Costing
Accurate heavy equipment costing allows businesses to:
- Enhance Budget Management: With precise figures, companies can allocate funds more effectively.
- Improve Decision Making: Understanding costs informs whether to buy, lease, or rent equipment.
- Increase Profitability: Keeping costs in check allows for better pricing strategies.
- Boost Competitiveness: Companies that manage equipment costs effectively can offer more competitive pricing.
Factors Affecting Heavy Equipment Costing
There are numerous factors that influence heavy equipment costing, which are essential to understand:
- Market Demand: The demand for construction and manufacturing services can drive equipment costs up or down.
- Brand and Model: Different manufacturers have varying price points based on quality and technology.
- Age and Condition: Newer machines typically come at a premium, while older models may be less expensive but come with higher maintenance costs.
- Technology: Advanced technology may improve efficiency but can also increase the initial investment.
- Geographic Location: Costs can vary significantly based on regional economic factors.
Amortization and Its Role in Heavy Equipment Costing
Understanding amortization is also vital in heavy equipment costing. Amortization involves spreading the cost of the equipment over its useful life. This not only affects the tax implications for businesses but also ensures that cash flow remains stable. For example, if a piece of equipment worth $100,000 is expected to last for five years, the annual amortization expense would be $20,000. This figure needs to be factored into the regular operational budget.
Rental vs. Purchase: A Cost Perspective
One of the key considerations in heavy equipment costing is whether to rent or purchase equipment. Here are some points to consider:
Purchasing Equipment
Pros:
- Long-term asset that can be used indefinitely.
- Potential resale value.
- Complete control over the equipment.
Cons:
- High upfront costs.
- Ongoing maintenance and repair responsibility.
- Depreciation leading to loss of value over time.
Renting Equipment
Pros:
- No large upfront expenses; pay as you use.
- Latest equipment access without the purchase commitment.
- Flexibility to adjust inventory based on project needs.
Cons:
- No ownership or asset value.
- Potentially higher long-term costs if rented for extended periods.
- Availability issues based on demand.
Best Practices for Managing Heavy Equipment Costs
To optimize heavy equipment costing, businesses can adopt several best practices:
- Regular Maintenance: Keep equipment in good working condition to avoid costly repairs.
- Strategic Purchasing: Buy at the right time, considering market trends and demand.
- Evaluate Usage: Analyze which pieces of equipment are used frequently and which are not.
- Invest in Training: Ensure operators are well-trained to minimize the risk of accidents and inefficiencies.
- Negotiate Costs: Always seek competitive pricing from suppliers.
Conclusion
Understanding heavy equipment costing is integral for businesses in transportation services, including town car service and vehicle shipping. When managed effectively, these costs not only affect company profitability but also enhance operational efficiency. Companies looking to excel in their field must prioritize understanding the comprehensive aspects of equipment expenditure as part of their financial strategy. Explore more about how you can effectively manage heavy equipment costs at elevationtransportservices.com.