Unlocking Efficiency in Manufacturing: The Power of Injection Molding Tools
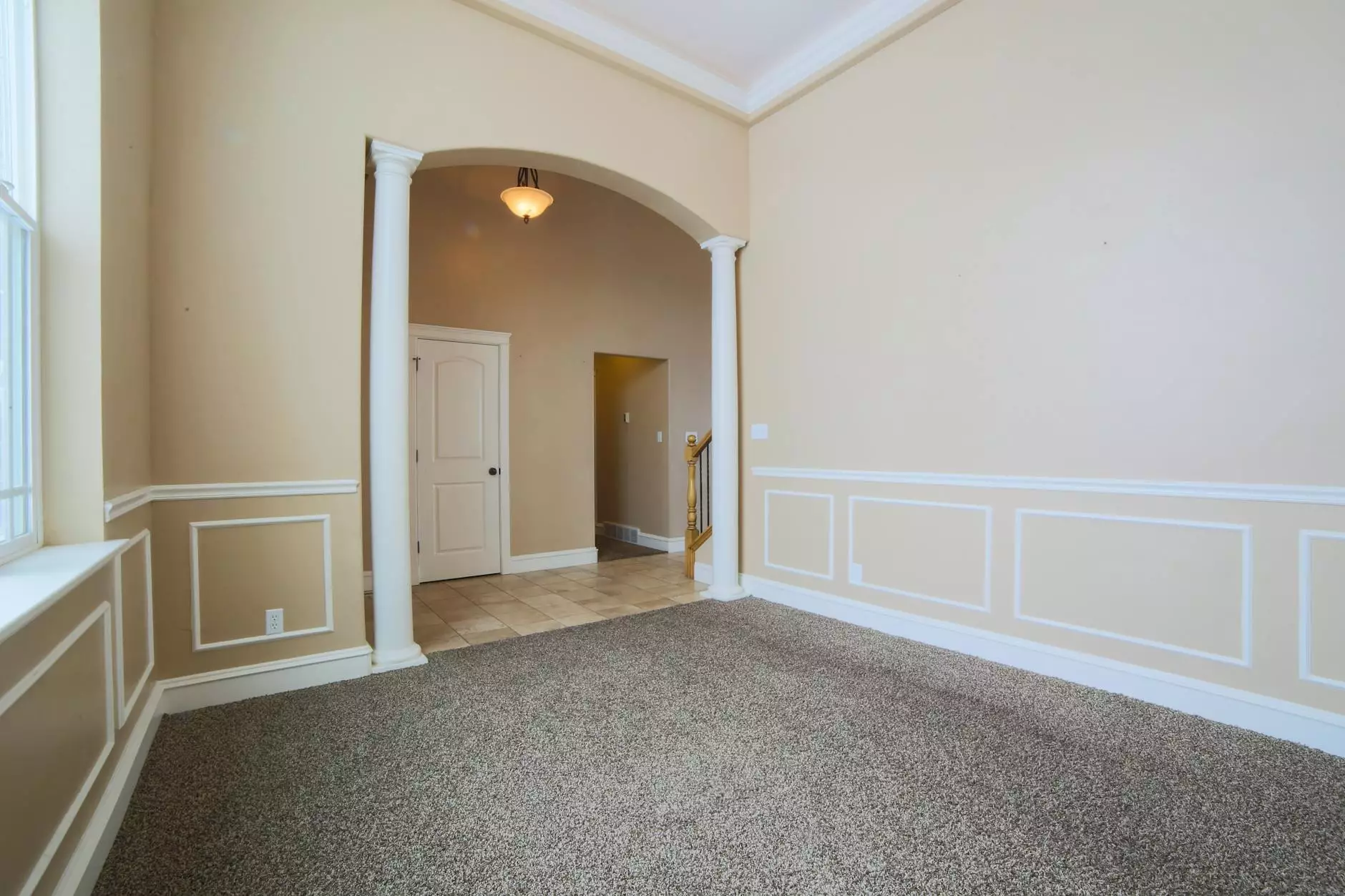
In the ever-evolving world of manufacturing, injection molding tools have emerged as a cornerstone for producing high-quality plastic parts at scale. These tools not only impact the efficiency of production processes but also play a significant role in determining the overall quality and cost-effectiveness of manufactured products. This article navigates the intricate landscape of injection molding tools and their pivotal role in modern industrial applications.
What are Injection Molding Tools?
Injection molding tools are specialized equipment used in the injection molding process, a method that allows manufacturers to produce complex shapes and designs with high precision. The process involves the injection of molten plastic material into a mold, where it cools and solidifies into the desired shape. The tools consist of various components, each meticulously engineered to ensure optimal performance. Key components of these tools include:
- Molds: The heart of the injection molding tool, molds define the shape and dimensions of the final product.
- Heating and cooling systems: These systems are crucial for maintaining the right temperatures during the injection process, ensuring efficient cycle times.
- Injection units: This component is responsible for injecting molten plastic into the mold with the right pressure and speed.
- Clamping units: Clamping units hold the mold halves together during injection and cooling.
The Importance of Injection Molding Tools
Injection molding tools are essential for several reasons:
1. High Precision and Accuracy
One of the most significant advantages of using injection molding tools is their ability to produce parts with an exceptional degree of accuracy. This precision is critical in industries such as automotive and aerospace, where even the slightest deviation from specifications can have severe consequences.
2. Cost-Effectiveness
While the initial investment in injection molding tools can be substantial, they offer significant cost savings in the long run. The high efficiency and speed of the injection molding process allow for mass production, reducing the cost per unit significantly.
3. Versatility
Injection molding tools can be utilized to produce a wide range of products, from simple household items to complex automotive components. Their adaptability makes them invaluable across various sectors.
Types of Injection Molding Tools
There are several types of injection molding tools, each designed for specific applications. Understanding these types can help manufacturers choose the right tool for their needs.
1. Single Cavity Molds
Single cavity molds are designed to produce one part per cycle. They are often used for products with high demand and uniformity, providing simplicity and efficiency in production.
2. Multi-Cavity Molds
Multi-cavity molds can produce multiple parts in a single cycle, enhancing productivity. They are ideal for high-volume production runs and are often used in industries with a high demand for identical parts.
3. Family Molds
Family molds are designed to produce different parts simultaneously. This flexibility allows manufacturers to diversify their product offerings without needing multiple separate molds.
Main Materials Used in Injection Molding Tools
The materials used in manufacturing injection molding tools are crucial for their performance and longevity. Common materials include:
- Steel: Known for its durability, steel molds are ideal for high-volume production runs.
- Aluminum: Lighter and less expensive than steel, aluminum molds are suitable for low to medium production volumes, offering a faster turnaround time.
- Composite materials: These materials combine the benefits of both steel and aluminum, providing a balance between durability and cost-effectiveness.
Key Advantages of Using High-Quality Injection Molding Tools
Investing in high-quality injection molding tools yields numerous advantages for manufacturers, including:
1. Enhanced Production Speed
Quality molds lead to faster cycle times, meaning manufacturers can produce more parts in a shorter period, thus meeting market demands swiftly.
2. Improved Product Quality
High-quality tools ensure consistency in dimensions and surface finishes, which enhances the overall quality of the final product. This consistency builds brand trust and customer satisfaction.
3. Reduced Waste and Sustainability
With precision engineering, high-quality injection molding tools minimize material waste. Additionally, the ability to recycle leftover materials contributes to sustainable manufacturing practices.
Choosing the Right Injection Molding Tool for Your Business
Selecting the right injection molding tools for your manufacturing needs involves several considerations:
1. Product Design and Complexity
The complexity of the product you intend to manufacture will largely dictate the type of mold required. More intricate designs may necessitate advanced multi-cavity or family molds.
2. Production Volume
Assessing your production volume is critical. For high volumes, investing in a robust steel mold might be the best choice, while a smaller production run might justify the use of an aluminum mold.
3. Material Compatibility
Ensure that the chosen mold material is compatible with the plastic resins you'll be using. Different materials respond differently to temperature and pressure, influencing the overall efficiency of the process.
Injection Molding Process: A Step-by-Step Overview
Understanding the injection molding process is essential for maximizing the benefits of injection molding tools. Here's a step-by-step overview:
Step 1: Material Preparation
The process begins with the preparation of the raw plastic granules, which are heated and melted in preparation for injection.
Step 2: Injection
The molten plastic is injected into the mold at high pressure, filling every cavity and ensuring complete shape formation.
Step 3: Cooling
Once the mold is filled, the material is allowed to cool and solidify. Cooling times can vary based on the material and the thickness of the part.
Step 4: Mold Opening and Ejection
After cooling, the mold opens, and the finished part is ejected. Ejection systems help ensure that the part is removed without damage.
Step 5: Finishing
Any excess material or imperfections are trimmed or processed to ensure each part meets quality standards before packaging.
Future Trends in Injection Molding Tools
The industry is poised for exciting changes, driven by technological advancements. Key future trends include:
1. Automation and Robotics
The integration of automation and robotics in the injection molding process promises increased efficiency and reduced labor costs.
2. 3D Printing and Additive Manufacturing
The rise of 3D printing technologies could revolutionize mold manufacturing, allowing for rapid prototyping and more complex mold designs that were previously unattainable.
3. Sustainable Practices
As environmental concerns grow, manufacturers are increasingly focusing on sustainable practices, such as using recyclable materials in both process and product design.
Conclusion: The Value of Investing in Quality Injection Molding Tools
In conclusion, understanding and investing in injection molding tools is crucial for any manufacturer looking to thrive in today’s competitive landscape. The benefits of precision, cost-effectiveness, and versatility make these tools indispensable for producing high-quality products. By leveraging advanced technologies and focusing on sustainability, businesses can position themselves at the forefront of innovation in manufacturing.
At Deep Mould, we specialize in providing high-end injection molding tools tailored to meet the specific needs of your business. Our commitment to quality, innovation, and customer satisfaction ensures that you receive the best products that boost your manufacturing efficiency and product quality.