Exploring Precision and Excellence in Metal Fabrication: The Power of Precise Molding
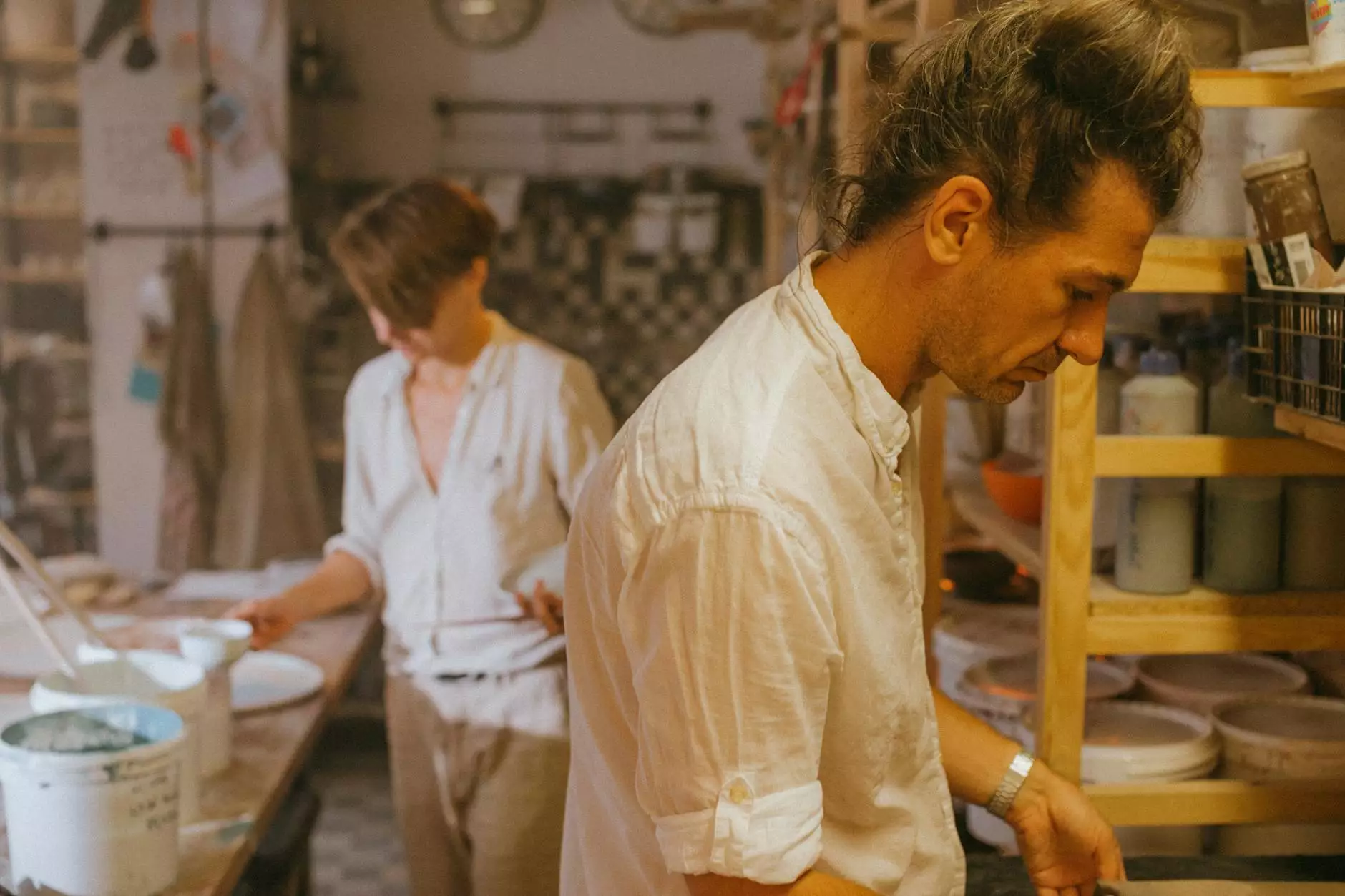
In the ever-evolving landscape of modern manufacturing, businesses are constantly seeking methods to enhance efficiency and maximize quality. One technique that has gained immense popularity and significance is precise molding. This article delves into the intricacies of precise molding in the realm of metal fabrication, showcasing its benefits and applications, while also examining how it can transform operational capabilities for businesses like deepmould.net.
Understanding Precise Molding
Precise molding refers to the highly controlled process of shaping materials, particularly metals, into desired forms with exceptional accuracy. This process is pivotal for industries where precision is paramount, including automotive, aerospace, and consumer goods manufacturing. The term encompasses various methodologies, including die casting, injection molding, and stamping, each designed to achieve high tolerances and complex geometries.
The Importance of Precision in Manufacturing
Precision in manufacturing minimizes waste, enhances product quality, and streamlines production times. For businesses focused on achieving excellence in their products, understanding the fundamentals of precise molding becomes essential.
- Reduced Waste: Exact molding processes limit excess material usage, contributing to sustainability.
- Increased Efficiency: Precise shaping reduces the need for additional machining, speeding up production cycles.
- Consistent Quality: High tolerance levels ensure that every piece produced meets stringent quality standards.
Applications of Precise Molding in Metal Fabrication
The versatility of precise molding allows its application across various sectors that heavily rely on metal fabrication techniques. Here are a few prominent industries that benefit significantly from incorporating precise molding into their manufacturing processes:
1. Automotive Industry
In the automotive sector, the demand for lightweight yet durable components is relentless. Precise molding techniques enable manufacturers to produce intricate parts such as engine blocks, chassis components, and decorative trims with unparalleled precision. This not only enhances vehicle performance but also contributes to fuel efficiency.
2. Aerospace Sector
The aerospace industry demands components that can withstand extreme conditions while maintaining structural integrity. Utilizing precise molding allows for the creation of complex components like turbine blades and fuselage structures, which must meet exacting specifications and undergo rigorous testing.
3. Consumer Electronics
From smartphones to home appliances, consumer electronics require components that are both lightweight and reliable. Precise molding ensures that casing and internal components fit perfectly, reducing the risk of failure and enhancing the user experience.
Key Benefits of Precise Molding in Metal Fabrication
The advantages provided by precise molding can redefine a company's production capabilities. Here’s a look at some of the primary benefits:
Cost-Effectiveness
Although the initial setup cost for precise molding processes can be higher, the long-term savings are significant. By minimizing material waste and reducing production time, businesses can lower their overall production costs.
Enhanced Product Durability
Products manufactured through precise molding often exhibit enhanced durability due to the optimized structural integrity of the molded parts. This translates to a longer lifespan and improved performance in demanding applications.
Rapid Prototyping and Shorter Lead Times
Precise molding allows for rapid prototyping, enabling businesses to test designs quickly and efficiently. This agility leads to shorter lead times, helping companies respond to market changes promptly.
Challenges of Precise Molding
While the benefits of precise molding are extensive, there are challenges that businesses must navigate:
- Initial Equipment Investment: The cost of machinery and technology for precise molding can be significant.
- Skilled Labor Requirement: Implementing precise molding techniques demands a workforce with specialized skills and training.
- Material Limitations: Certain materials may not be suitable for all types of precise molding methods, constraining options.
Choosing the Right Metal Fabricator
For businesses looking to leverage the advantages of precise molding, selecting the right metal fabricator is crucial. The fabricator's experience, technology, and quality assurance practices play vital roles in ensuring successful outcomes.
Factors to Consider When Selecting a Metal Fabricator
To make an informed decision, consider the following:
- Experience and Expertise: Look for a fabricator with a proven track record in precise molding techniques relevant to your industry.
- Quality Assurance Processes: Ensure that the fabricator maintains stringent quality controls to minimize defects.
- Technological Capabilities: Advanced molding and fabrication technologies can significantly impact the precision and quality of outputs.
- Customer Reviews: Feedback from previous clients can provide insights into the fabricator's reliability and service quality.
Future Trends in Precise Molding
The future of precise molding looks promising, with advancements in technology shaping the landscape. Areas to watch include:
1. Automation and Robotics
The incorporation of automation in precise molding processes is set to enhance production efficiency and consistency. Robotics can expedite repetitive tasks, allowing human workers to focus on more complex issues.
2. Innovations in Materials
As material science evolves, the development of new alloys and composites will expand the possibilities for precise molding. These materials can offer enhanced performance characteristics that meet emerging industry demands.
3. Sustainability Initiatives
With an increasing focus on sustainability, the adoption of eco-friendly practices in precise molding is gaining momentum. Techniques that reduce energy consumption and waste while optimizing resource use will become industry standards.
Conclusion
As we navigate the complexities of modern manufacturing, precise molding stands out as a key methodology that can significantly impact product quality and production efficiency. Businesses that harness the power of precise molding not only improve their operational capabilities but also position themselves for sustainable growth in an increasingly competitive market.
By understanding the intricacies of precise molding and selecting the right partners in metal fabrication, companies can achieve unparalleled quality, efficiency, and innovation in their manufacturing processes. Embrace the future of metal fabrication and let DeepMould.net be your trusted ally in achieving excellence.