The Critical Role of an Injection Mold Maker in Modern Manufacturing
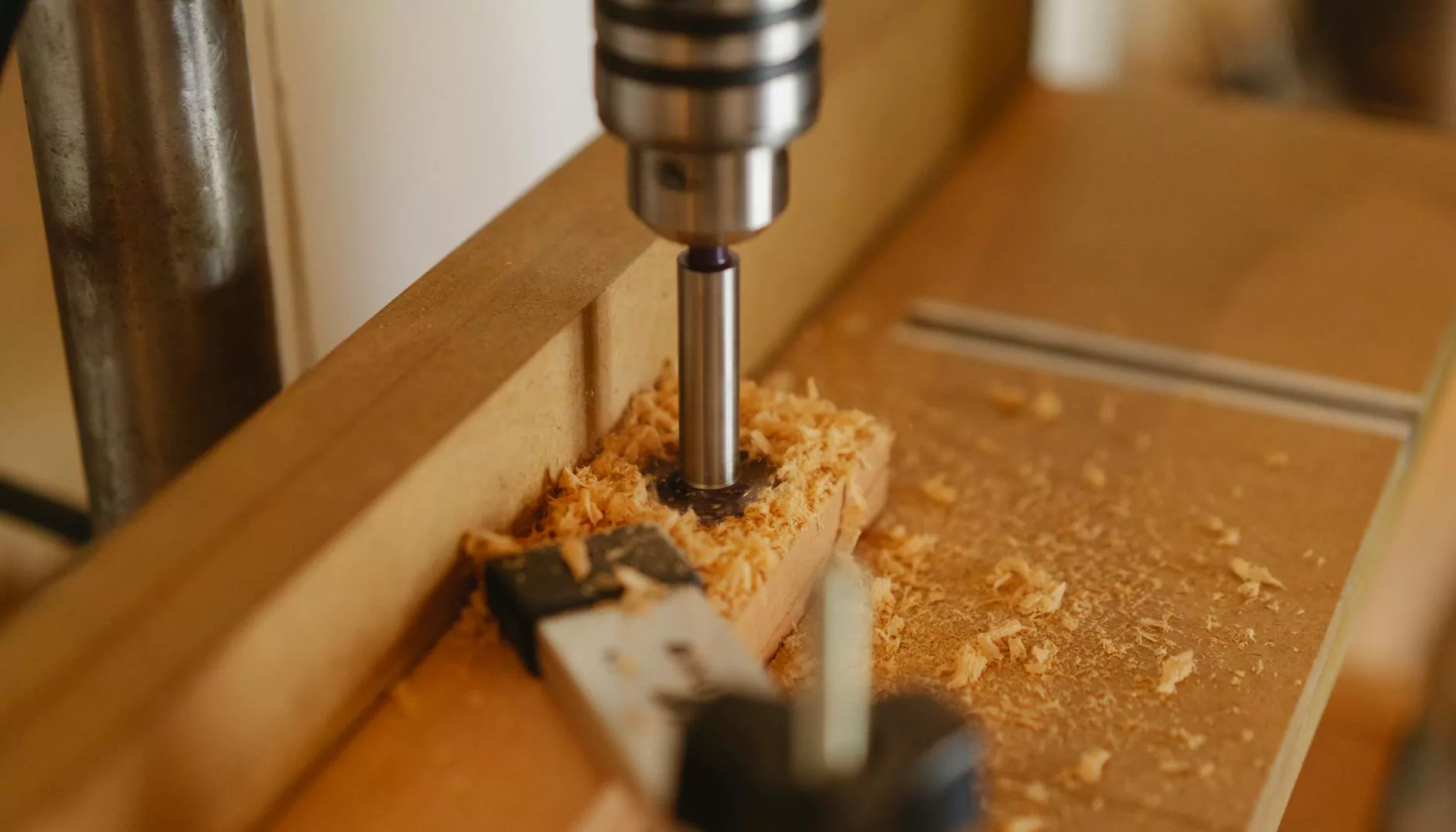
In today's fast-paced manufacturing environment, the demand for precision and efficiency has never been greater. One of the key players in this realm is the injection mold maker. These skilled craftsmen are vital to the production of a wide range of products, from everyday household items to complex industrial components. This article delves deep into the world of injection mold making, exploring its importance, the skills required, and how it aligns with the broader category of metal fabricators.
What is an Injection Mold Maker?
An injection mold maker specializes in designing and fabricating molds that are used in the injection molding process. This process involves injecting molten material—most commonly plastics—into a mold to create products ranging from simple components to intricate designs. The role of an injection mold maker requires both creativity and technical prowess, combining artistry with engineering finesse.
The Importance of Injection Molding in Manufacturing
Injection molding is one of the most widely used manufacturing processes in the world. It is favored for its ability to produce components with outstanding precision and repeatability. Here are several reasons why injection molding is integral to modern production:
- Efficiency: Injection molding allows for rapid production cycles, which can significantly reduce lead times and increase output.
- Complex Geometries: It enables the creation of complex shapes and designs that would be challenging to fabricate using other methods.
- Material Versatility: A variety of materials can be used, including thermoplastics, thermosets, and elastomers.
- Cost-Effectiveness: While the initial investment in molds can be high, the scalability and reproducibility make it cost-effective for large production runs.
- Environmental Considerations: Injection molding can contribute to sustainable practices, as recycled materials can be used in the process.
Key Skills of an Injection Mold Maker
Becoming a successful injection mold maker requires a blend of skills, experience, and education. Here are some key competencies that are essential in this profession:
1. Technical Knowledge
Understanding the principles of thermodynamics, material science, and mechanical engineering is crucial. Mold makers must be well-versed in the characteristics of different materials and their behavior when heated and cooled.
2. CAD/CAM Proficiency
Computer-Aided Design (CAD) and Computer-Aided Manufacturing (CAM) are cornerstone technologies in mold making. Proficiency in these tools allows for precise design and simulation of molds before physical production begins.
3. Attention to Detail
Mold makers must have a keen eye for detail. Any imperfections in the mold can lead to defects in the final product, resulting in increased costs and wasted materials.
4. Problem-Solving Skills
The ability to troubleshoot issues that may arise during the mold-making process is invaluable. Mold makers often need to find solutions quickly to keep production on schedule.
5. Manual Dexterity and Craftsmanship
Despite the advancements in automation and technology, the role of skilled craftsmanship remains irreplaceable. Mold making often involves intricate manual processes that require dexterity and an artistic touch.
The Injection Mold Manufacturing Process
The journey of creating a mold begins with a clear understanding of the product design. Below is a straightforward overview of the typical steps involved in the injection mold manufacturing process:
Step 1: Product Design
The process begins with a detailed product design, which is often created using CAD software. The design must consider the final product's dimensions, weight, and functional requirements.
Step 2: Mold Design
Once the product design is complete, the mold's design process begins. This includes selecting the type of mold (e.g., single-cavity vs. multi-cavity) and planning for features like cooling channels and ejector pins.
Step 3: Material Selection
The choice of material for the mold itself is crucial. Steel and aluminum are common choices due to their durability and thermal conductivity, but the choice often depends on the volume of production and the type of resin used.
Step 4: Machining
This is where the actual mold manufacturing takes place. Precision machining techniques, such as milling, EDM (electrical discharge machining), and grinding, are employed to create the mold based on the design specifications.
Step 5: Assembly
After the individual parts of the mold have been manufactured, they are meticulously assembled. This step may involve fitting inserts and ensuring that moving components function smoothly.
Step 6: Testing and Refinement
Before the mold is put into production, it undergoes rigorous testing. Initial injection trials are conducted to check for defects and verify that it meets the designed specifications. Adjustments may be necessary to fine-tune the mold.
Challenges Faced by Injection Mold Makers
While the job of an injection mold maker can be rewarding, it also comes with challenges that professionals in the field must navigate:
- Rapid Advancements in Technology: Keeping up with the latest manufacturing technologies and materials can be daunting.
- High Competition: The industry can be competitive, requiring constant improvement and innovation to stay ahead.
- Cost Management: Balancing quality and cost in mold production is crucial, especially in industries where margins are tight.
- Customer Expectations: Meeting the increasing demand for faster turnaround times without compromising quality is a continuous challenge.
The Future of Injection Mold Making
The future of the injection mold maker profession looks bright, with several key trends on the horizon:
1. Embrace of Automation
Automation technologies, including robotics and AI, are beginning to play a significant role in the manufacturing process. Mold makers must adapt to these changes while finding ways to leverage technology to enhance efficiency.
2. Advanced Materials
As new materials emerge that offer better performance and sustainability, mold makers will need to expand their expertise to include these advanced options.
3. Increased Sustainability Efforts
With growing awareness of environmental issues, there is an increasing demand for eco-friendly practices in manufacturing. Mold makers will play a crucial role in developing sustainable products and processes.
4. Customization and Shorter Runs
With the rise of personalized products, there is a growing trend towards short-run production and customization, which requires exceptional adaptability from injection mold makers.
Conclusion
As an essential component of the manufacturing landscape, injection mold makers are poised to remain critical to the success of various industries. Their blend of artistry, technical skill, and problem-solving ability makes them invaluable in producing high-quality products. As the industry evolves, those who embrace continuous learning and innovation will lead the way in shaping the future of manufacturing. By partnering with experienced professionals in the field, such as those at DeepMould.net, businesses can ensure they stay at the forefront of product development and manufacturing excellence.
Remember: The precision and quality of the molds created by an injection mold maker are a direct reflection of the final products. Investing in skilled mold makers is investing in the future of your production capabilities.