Understanding the Role of a Plastic Injection Manufacturer in Today's Market
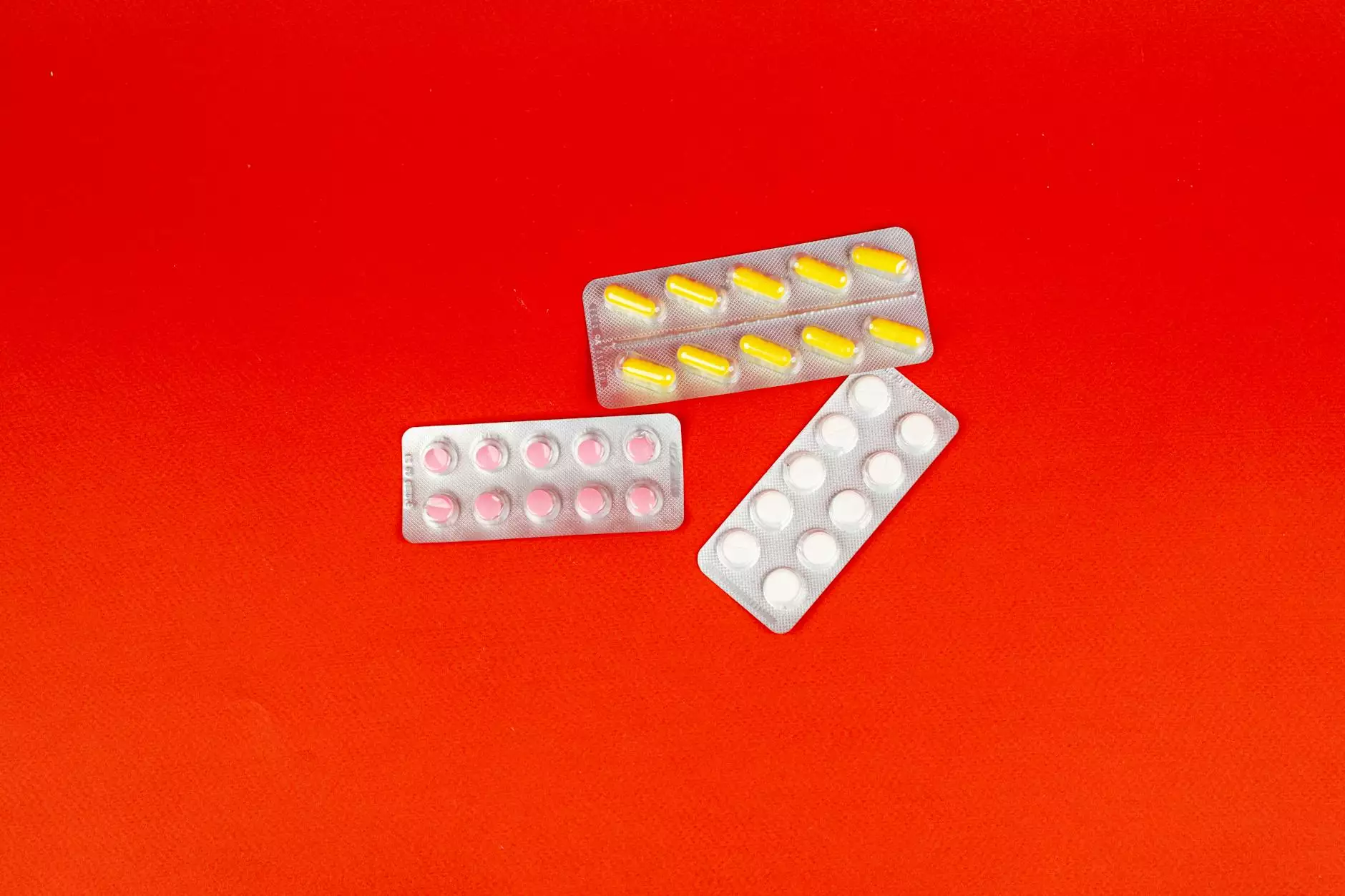
In the modern manufacturing landscape, the term plastic injection manufacturer resonates with innovation, efficiency, and unparalleled precision. This method of production, characterized by its ability to mold complex shapes and designs, has revolutionized the creation of plastic components across numerous industries, including automotive, consumer goods, and electronics. In this article, we will delve deep into the world of plastic injection manufacturing, exploring its processes, benefits, and significance in the category of metal fabricators.
The Process of Plastic Injection Molding
At its core, the process of plastic injection molding combines science and art to create intricate products. Below, we will outline the fundamental steps involved in this state-of-the-art manufacturing process.
1. Material Selection
The first step in the plastic injection molding process is the selection of the right type of plastic material. Different projects require specific plastic types based on factors like:
- Durability: Will the product be subjected to harsh conditions?
- Flexibility: Does the part need to bend or flex without breaking?
- Heat Resistance: Will the end product be exposed to heat?
- Transparency: Is clarity an aesthetic requirement?
2. Designing the Mold
After selecting the appropriate material, the next phase is designing the mold. This involves:
- Creating detailed 3D models.
- Considering the mechanics of how the plastic will fill the mold.
- Ensuring that mold design accommodates for any post-processing needs.
3. Injection Process
Once the mold is designed and built, the process of injection begins. Here's how it works:
- The selected plastic material is heated until it reaches a molten state.
- This molten plastic is then injected into the mold under high pressure.
- The mold is allowed to cool, solidifying the plastic into the desired shape.
- The mold opens, and the newly created plastic part is ejected.
4. Quality Control and Finish
After the parts are produced, they undergo rigorous quality control to ensure they meet the required standards. This can include:
- Visual inspections for defects.
- Dimensional checks to confirm specifications.
- Functional testing to ensure performance benchmarks are met.
Advantages of Plastic Injection Molding
Choosing to work with a plastic injection manufacturer offers numerous advantages that can significantly benefit businesses.
1. High Efficiency
One of the standout features of this manufacturing process is its speed and efficiency. Products can be produced in high volume with relatively little labor, reducing overall production time and costs.
2. Design Flexibility
The technology allows for the creation of complex parts that might be impossible with traditional manufacturing techniques. This flexibility is a cornerstone feature for companies needing innovative designs.
3. Cost-Effectiveness
For high-volume productions, the cost per unit decreases significantly because the initial setup costs are spread over the large number of products manufactured. This makes it a financially attractive option for many businesses.
4. Material Versatility
A wide variety of plastic materials can be used, from standard polymers to high-performance thermoplastics. This means that plastic injection manufacturers can cater to diverse industrial needs.
Applications of Plastic Injection Molding
Plastic injection molding is embraced across multiple industries, which showcases its adaptability and effectiveness. Some prominent applications include:
1. Automotive Components
In the automotive industry, many interior and exterior components—such as dashboards, panels, and trims—are produced using injection molding. This process allows for parts that are both lightweight and durable, enhancing fuel efficiency without compromising safety.
2. Consumer Goods
Everyday items, from bottles to toys, are often manufactured using injection molding techniques. The ability to produce intricate designs at a low cost makes this process ideal for high-demand consumer products.
3. Electronics
Electronics casings and components also benefit from precision injection molding. The exacting standards required in electronic assembly are perfectly met through this method, ensuring reliability in performance.
Choosing the Right Plastic Injection Manufacturer
When selecting a plastic injection manufacturer, it is crucial to consider several factors to ensure that your production needs are met with excellence:
1. Experience and Expertise
Look for a manufacturer with years of experience in the industry. Their expertise in handling various materials and intricate designs can make a significant difference in product quality.
2. Technology and Equipment
State-of-the-art technology streamlines the injection process, improving efficiencies and reducing defects. Ensure your chosen manufacturer utilizes the latest equipment.
3. Quality Assurance Practices
A reputable manufacturer will have strict quality control procedures in place. Inquire about their quality assurance processes to understand how they maintain high standards.
4. Customer Support
Reliable customer service can facilitate smoother operations. Effective communication is essential in addressing any challenges that may arise during the manufacturing process.
The Future of Plastic Injection Manufacturing
As industries continue to evolve, the world of plastic injection manufacturing is also adapting. Innovations in materials, automated processes, and sustainable practices are shaping the future of this sector.
1. Sustainability Initiatives
With a growing emphasis on sustainability, many manufacturers are exploring eco-friendly materials and recycling processes. The integration of biodegradable plastics and recycling post-consumer waste into production signifies a significant change in industry practices.
2. Advanced Robotics and Automation
The rise of automation in manufacturing processes leads to faster production speeds and reduced human error. Robotics is becoming more common, allowing for more intricate and precise designs to be produced with lower operational costs.
Conclusion
Being a plastic injection manufacturer represents not just a significant role in the production chain but also an avenue for innovation and quality enhancement in manufacturing. As businesses in various sectors adopt injection molding for their production needs, understanding the intricacies of this method becomes increasingly vital. By focusing on efficiency, design flexibility, and quality, companies can gain a substantial competitive edge in today's fast-paced market.
For more information and to explore high-quality manufacturing solutions, consider visiting deepmould.net, where you can find expert insights and services tailored to your needs.