The Evolution of Laser Welders in Metal Fabrication
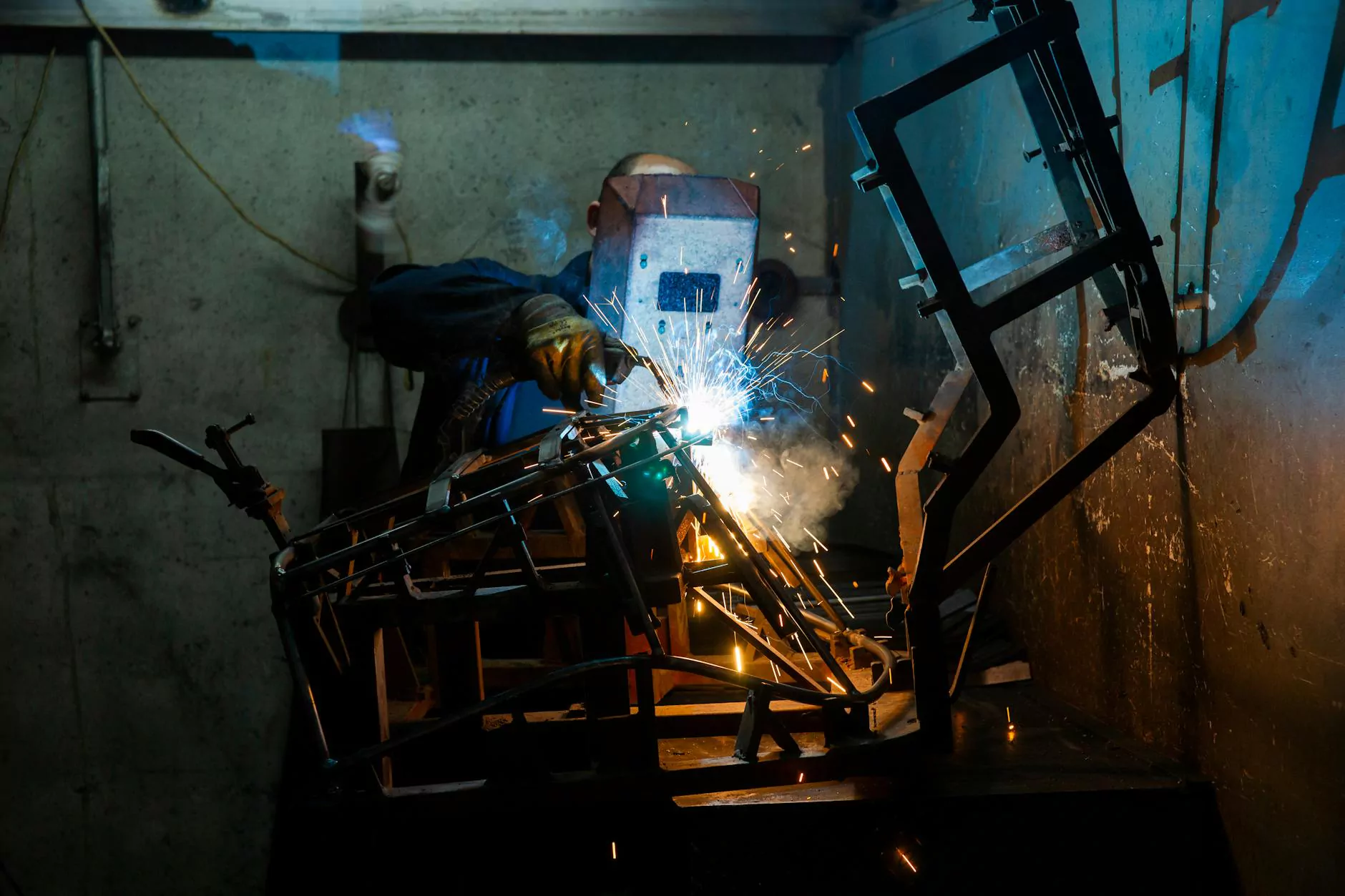
In the realm of Metal Fabricators, the laser welder has emerged as a game-changer, transforming traditional welding methods into highly efficient and precise processes. This advanced technology provides numerous benefits for businesses looking to streamline their fabrication operations.
Enhanced Precision and Accuracy
Laser welders offer unmatched precision and accuracy, allowing metal fabricators to create intricate designs and weld components with utmost detail. The focused beam of the laser ensures welding is done with minimal heat-affected zones, resulting in clean and flawless joints.
Increased Efficiency and Productivity
With the speed and accuracy of laser welding, Metal Fabricators can significantly increase their productivity levels. Tasks that used to take hours can now be completed in a fraction of the time, leading to faster turnaround times and enhanced efficiency.
Cost Savings and Sustainability
By investing in laser welders, businesses in the Metal Fabrication industry can achieve cost savings in the long run. The precision of laser welding reduces material wastage, while the energy-efficient nature of the process contributes to sustainability initiatives.
Improved Quality and Strength
The high power and control of laser welders result in welds that exhibit superior quality and strength. This ensures that fabricated metal components are durable and resistant to wear and tear, meeting the highest industry standards.
Conclusion
As Metal Fabricators continue to explore innovative technologies, incorporating laser welders into their operations has become essential for staying competitive in the market. The benefits of precision, efficiency, cost savings, and quality make laser welders a must-have tool in modern fabrication processes.